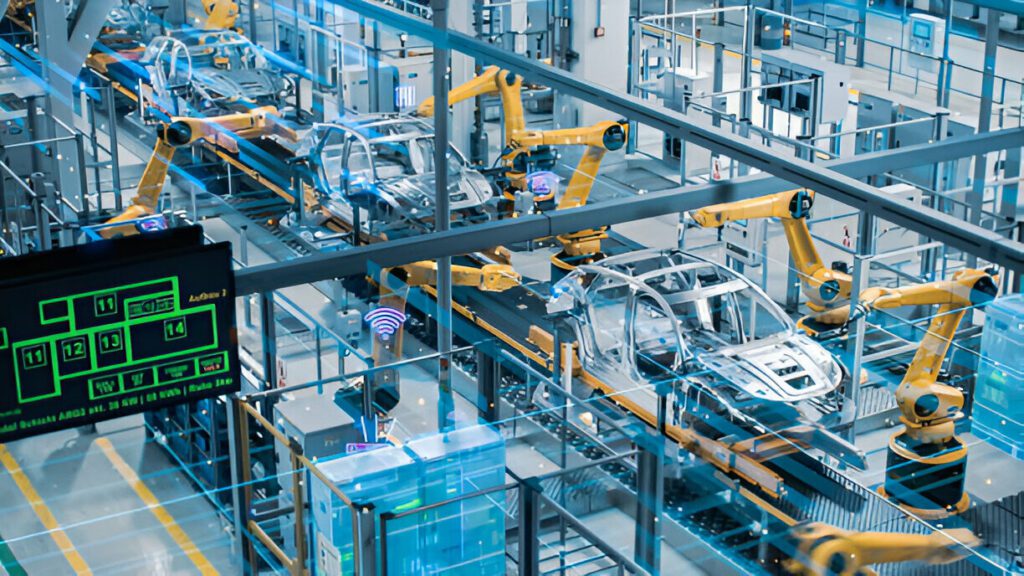
The manufacturing landscape is undergoing a metamorphosis driven by artificial intelligence (AI). Imagine production lines that self-adjust in real-time, machinery predicting its own maintenance needs, and intelligent systems streamlining every facet of the supply chain. This isn’t science fiction; it’s the present, powered by AI’s transformative capabilities. However, integrating AI into manufacturing isn’t a walk in the park. Two critical roadblocks stand out: data and talent.
Data Deluge: A Double-Edged Sword
Manufacturing is awash in a data deluge. Sensors, Internet of Things (IoT) devices, and interconnected machinery generate an information flood, offering unparalleled insights into production. However, managing this data tsunami presents a significant challenge. Traditional systems struggle with the sheer volume, straining storage capacities and hindering processing.
But quantity isn’t the only concern. Data quality is paramount. Imagine feeding “garbage” into a complex AI model – the results will be equally messy. Inaccurate, inconsistent, or incomplete data undermines AI’s effectiveness. Manufacturers must prioritize data hygiene – cleaning, standardizing, and enriching data to ensure reliable AI predictions.
Data silos pose another challenge. Production data often resides in isolated pockets across departments, making it difficult to obtain a holistic view of operations. Bridging these silos requires a unified data environment, often necessitating overhauls of existing IT infrastructure – a significant undertaking.
As manufacturing systems become increasingly interconnected, data security and privacy become paramount. Cyber threats pose substantial risks to sensitive production data, potentially leading to devastating operational disruptions. Striking a balance between accessibility and robust security measures is essential. Manufacturers must implement stringent cybersecurity practices to safeguard data, comply with regulations, and maintain trust with stakeholders.
Shaping the Data: From Raw Input to Actionable Insights
The effectiveness of AI hinges on the quality of data it ingests. Data preparation plays a crucial role, and cleaning takes center stage. Removing inaccuracies, handling missing values, and eliminating inconsistencies are essential tasks that ensure reliable results. Standardization ensures data from diverse sources speaks the same language, facilitating seamless integration and analysis.
Feature engineering is another critical step. This process transforms raw data into meaningful features that enhance AI performance. It involves selecting relevant variables, modifying them to highlight important patterns, or even creating entirely new features that unlock valuable insights. Effective feature engineering can significantly boost the predictive power of AI models, leading to more accurate and reliable outcomes.
Anomaly detection is also crucial for maintaining data quality. Identifying outliers and unusual patterns helps manufacturers address potential errors or issues that might otherwise go unnoticed. These anomalies can indicate problems with data collection or reveal important trends that require further investigation, ultimately ensuring the reliability of AI predictions.
Supervised learning models rely heavily on data labeling – the time-consuming yet essential process of annotating data with relevant tags or labels. Labeled data provides the necessary context for AI systems to understand and predict outcomes accurately, making it a cornerstone of successful AI deployment.
The Talent Conundrum: Building the AI-Ready Workforce
The talent shortage in manufacturing AI poses a significant hurdle. Finding professionals with a deep understanding of both AI and the intricacies of manufacturing processes is a major challenge. The skills gap – the lack of expertise in AI, machine learning, and data science – hinders widespread AI adoption.
Data scientists, machine learning engineers, and domain specialists are the key players in the manufacturing AI game. Data scientists decipher the complex language of data; machine learning engineers design and deploy AI models; and domain specialists ensure AI solutions align seamlessly with manufacturing challenges. A successful AI integration strategy requires a winning combination of these skillsets.
However, attracting and retaining these talented professionals is fiercely competitive, especially with large tech companies offering lucrative compensation packages. This can be particularly challenging for smaller manufacturing firms.
Bridging the Talent Gap: Strategies for Success
Addressing the AI talent gap necessitates a multifaceted approach. Upskilling the existing workforce is a powerful strategy. Manufacturers can equip their employees with essential skills by offering training programs, workshops, and certifications in AI and related technologies. Fostering a culture of continuous learning and professional development not only bridges the skills gap but also boosts employee retention.
Collaboration with academic institutions is another key strategy. Partnering with universities to design AI-specific curricula, offering internships, and engaging in joint research projects can create a pipeline of skilled professionals. These partnerships provide students with practical experience, while manufacturers benefit from a pool of qualified talent and collaborative research opportunities that drive innovation.
Leveraging external expertise is another effective approach. Outsourcing AI projects to specialized firms or collaborating with external consultants allows manufacturers to access advanced technologies and skilled professionals without extensive in-house expertise. Additionally, crowdsourcing platforms like Kaggle can connect manufacturers with a global pool of data scientists and machine learning experts to solve specific AI challenges.
The Future of Manufacturing is Now
Several leading manufacturers are reaping the benefits of AI. General Electric (GE) has successfully implemented AI-driven predictive maintenance, analyzing sensor data to predict equipment failures before they occur. This proactive approach has significantly reduced downtime and maintenance costs, while extending machinery lifespan.
Similarly, Bosch has leveraged AI for demand forecasting, optimizing inventory levels to reduce costs and improve order fulfillment. Additionally, AI-powered quality control systems have been implemented by companies like Siemens, leading to real-time defect detection and a 15% increase in production efficiency.
In conclusion, AI is revolutionizing the manufacturing landscape. By overcoming data and talent challenges, manufacturers can unlock the transformative potential of AI. Investing in high-quality data practices, upskilling the workforce, and collaborating with external experts are key strategies for achieving unmatched efficiency, innovation, and competitiveness. Embracing AI technology empowers manufacturers to drive productivity and operational excellence, paving the way for a new era of intelligent manufacturing.